How do manufacturers ensure that every packet of chips, every bottle of medicine, and even entire pallets of goods meet precise weight requirements? Checkweigher, a machine that verifies weights in real time, makes this possible.
But how exactly do they work, and why are they essential across industries like food processing, pharmaceuticals, and logistics? This blog breaks down the definition, applications, and working principle of checkweighers.
What is a Checkweigher?
A checkweigher is an automatic or manual machine designed to measure the weight of packaged goods. Usually, it is located at the end of a production line to ensure that every product meets predefined weight specifications.
Suppose a package falls outside the acceptable weight range. It could be either too light or too heavy. Then, the checkweigher rejects it from the production line. Or, it may flag it for further inspection.
Unlike static weighing, checkweighers operate dynamically. This means they weigh products while they are moving on a conveyor belt. The result is fast and efficient quality control. Moreover, some advanced checkweighers can even weigh over 500 items per minute. However, this capability depends on package size and accuracy needs.
Checkweighers are often integrated with metal detectors and X-ray machines. This allows manufacturers to inspect products for additional quality concerns, such as missing components or contaminants. For this reason, it is a necessary tool for ensuring product consistency and compliance with industry regulations.
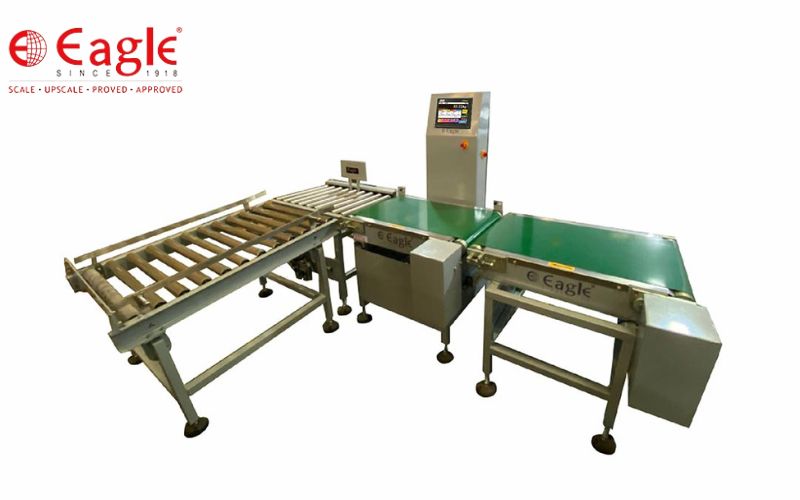
Uses of a Checkweigher
Checkweighers are commonly found in food processing, pharmaceutical, chemical, logistics, and manufacturing industries. Why? Because precision is non-negotiable in these fields. Here are some of the key ways they are used:
1. Ensuring Product Weight Compliance
In certain industries like food and pharmaceuticals, even slight deviations from the weight of packaged goods can lead to regulatory issues or customer dissatisfaction. So, making sure that the weight of those goods remains within acceptable limits is one of the primary functions of a checkweigher.
2. Detecting Missing Components
Checkweighers help identify missing parts in packaged kits. For example, in electronics manufacturing, a checkweigher can detect if a cell phone package is missing its charger or user manual. This prevents incomplete shipments from reaching customers.
3. Monitoring Production Quality
In industries like metalworking and plastics, checkweighers help in quality control. It verifies that the correct amount of material has been used. For example, in bearing manufacturing, a checkweigher ensures that the final product has the right weight. This confirms that the machining process has removed the necessary amount of metal.
4. Optimizing Poultry and Meat Processing
In poultry processing plants, birds are weighed before and after processing. This helps manufacturers determine if too much water has been absorbed during washing. This ensures that customers receive the correct meat weight and not excess water weight.
5. Regulating Packaging Speed and Spacing
A high-speed checkweigher can adjust the pace of products on a conveyor belt. It can increase or decrease the spacing between items before they reach a packaging machine. This is an important function for improving the efficiency of automated boxing or wrapping systems.
6. Preventing Product Giveaway
Overfilling a package might seem harmless. However, in high-volume production, even a few grams extra per item can lead to huge financial losses. Checkweighers help companies maintain precise weight limits to decrease product giveaways.
7. Shipment Verification and Tracking
Checkweighers are widely used in logistics and warehousing. They help count packages and measure total pallet weight. They even generate shipping labels. Furthermore, some checkweighers integrate barcode scanners to verify shipments. This way, they ensure no items are missing or tampered with during transit.
8. Sorting and Classification
In specific industries like agriculture, produce is graded based on weight. Similarly, in logistics, packages are sorted for shipping. In these industries, checkweighers classify products into different weight categories for sorting.
Principle of Operation: How a Checkweigher Works
Checkweighers operate using a combination of hardware and software to measure and analyze the weight of passing items. Here’s how these machines work:
1. Weighing the Product
The product moves onto the checkweigher’s weighing platform. Then, a load cell sensor detects its weight. After that, it converts the weight into an electrical signal.
2. Data Processing and Comparison
The weight measurement is sent to the checkweigher’s internal computer, also called a controller. It compares the weight against a predefined target range stored in its memory.
3. Decision-Making and Actions
If the weight is within the acceptable range, the product continues down the production line. If the weight is too low or too high, the system flags the product for removal. This is usually done using a rejection mechanism, such as:
- Air jets: Blowing the product off the line
- Pushers: Physically moving the item aside
- Diverter arms: Guiding the product into a separate area
4. Additional Features
Many checkweighers use indicator lights to signal whether a product is within the correct weight range. Usually, the green indication means “correct,” and the red indication means “reject.”
Modern checkweighers often integrate with packaging machines, labeling systems, and quality control software. This helps with hassle-free data collection and process optimization for better efficiency and accuracy.
Some advanced models trigger alarms to correct weight inconsistencies in real time. Few can even automatically adjust filling systems.
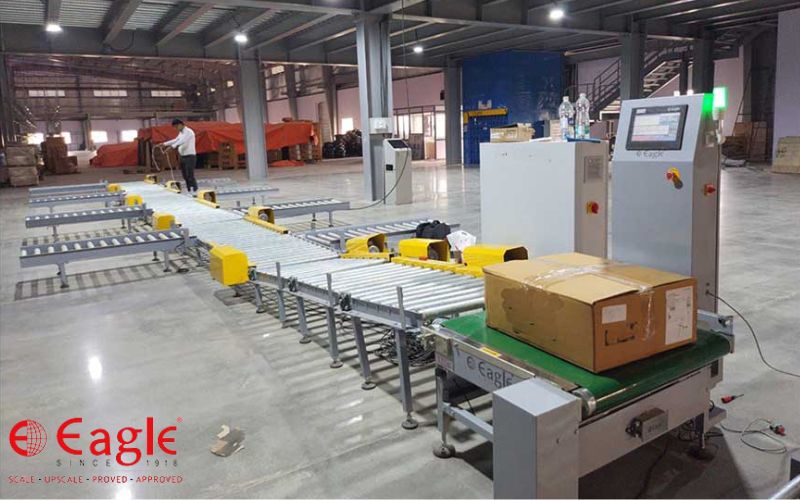
Conclusion
Checkweighers are integral in manufacturing, logistics, and quality control. They ensure that every product meets the correct weight specifications. They also detect missing components. On top of that, they make packaging and shipping processes simpler, well-run, and more efficient.
From food and pharmaceuticals to logistics and industrial manufacturing, these machines keep businesses running smoothly while preventing costly mistakes. As automation and Industry 4.0 continue to evolve, integrating checkweighers with data analytics and AI-driven systems will lead to even greater efficiencies.
If you’re looking to improve your production line’s precision and compliance, now is the time to explore the right checkweigher solution for your needs.
At Eagle Scales, we house solutions for every weighing application. With a 100-year legacy of providing the finest quality products, you will find everything you need — be it a baby weighing scale, commercial weighing scale, or kitchen scales. Explore our products here.